A Practical Guide to Off-Site Construction for Oak-Framed Buildings
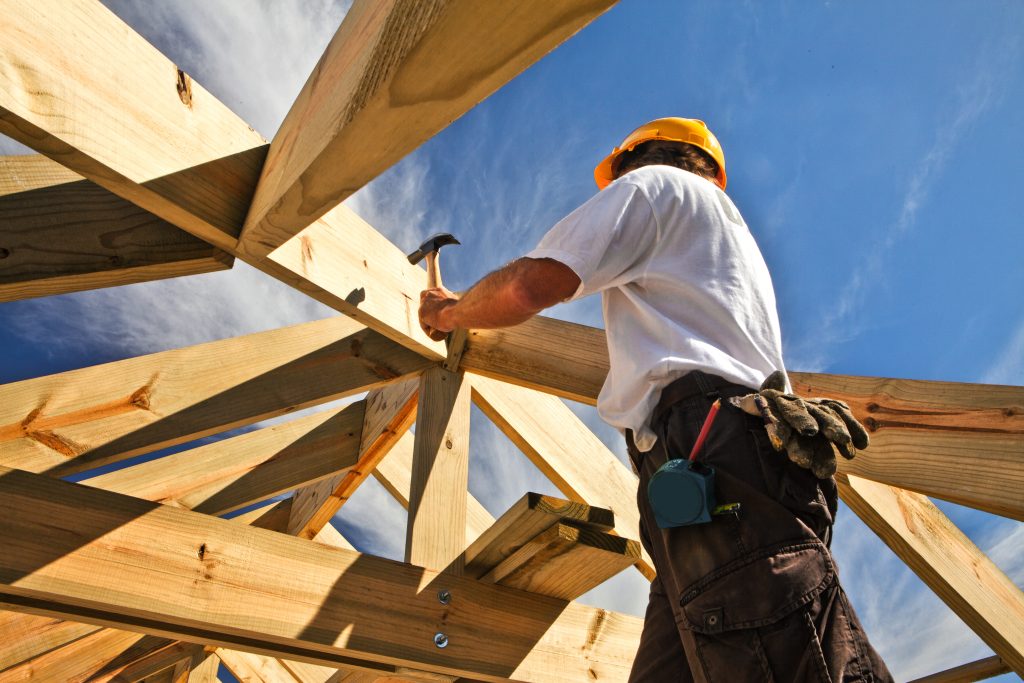
From garden rooms to full extensions, how your oak-framed structure is built matters just as much as what it’s made from. One increasingly popular method is off-site construction – a smarter, workshop-led approach that brings greater control and efficiency to your oak frame project.
What Is Off-Site Construction?
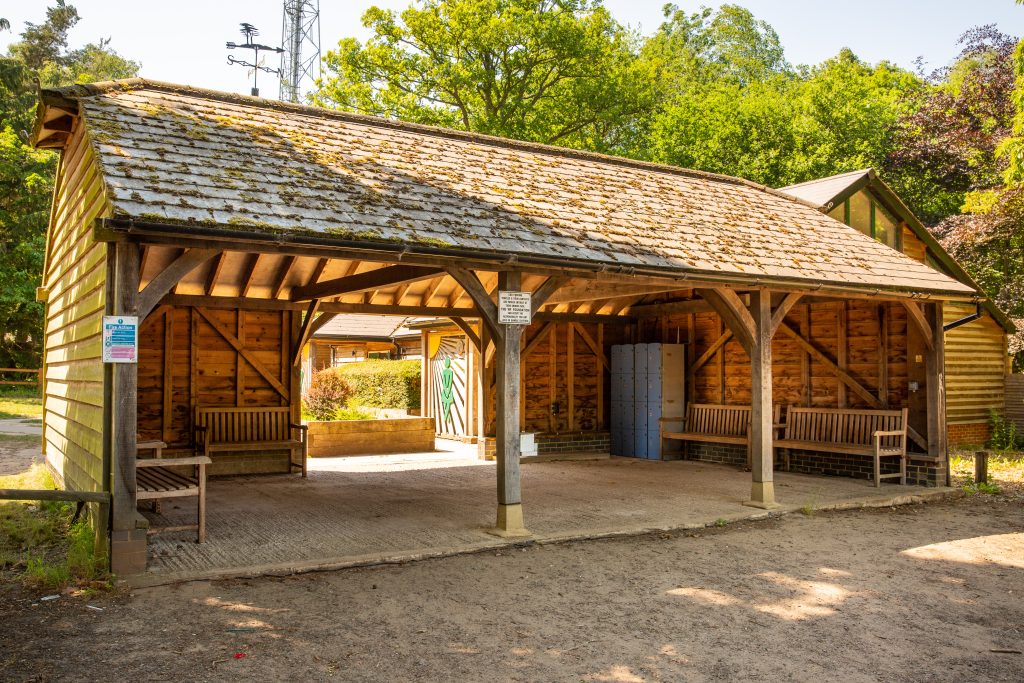
Off-site construction refers to the process of manufacturing and assembling an oak frame away from the final build site – typically within a dedicated workshop environment. Unlike traditional on-site builds, where frames are constructed piece by piece outdoors, off-site methods involve pre-cutting, shaping, and dry-assembling every component in controlled conditions.
This approach allows craftsmen to ensure that joints fit perfectly, alignment is spot on, and all elements come together exactly as intended. Once fully pre-assembled and checked, the frame is then disassembled, transported to site, and quickly re-erected.
Why Off-Site Construction Is a Superior Way to Build

In short, off-site construction removes much of the uncertainty from the build phase, delivering a smoother, safer, and more straightforward experience for everyone involved.
For you and your property, it means less disruption, more confidence in the final fit, and a build process that feels far more predictable from start to finish.
The Quality Assurance Benefits
Dry-fitting each oak frame in the workshop allows any design or fit issues to be identified and corrected long before the frame reaches your home. This step is key to ensuring that every joint slots together as it should, avoiding last-minute fixes that could compromise the structure or slow down the build.
It can also reach a level of finish that’s hard to achieve outdoors. Working in a controlled space means the oak can be fully planed, joints can be fine-tuned, and visual elements like curved braces are carefully crafted and checked for symmetry.
Time and Cost Efficiency
One of the most practical benefits of off-site construction is the reduction in time spent on site. Because the entire oak frame has already been dry-built and checked before delivery, the on-site assembly process is significantly quicker. What might take weeks using traditional methods can often be completed in a matter of days.
This speed can also translate into cost savings. Shorter build times mean fewer labour hours, less reliance on trades being available for extended periods, and reduced risk of weather delays causing costly interruptions. Wet or windy conditions are far less of a concern when the bulk of the build has already been completed under cover.
Ease of Installation and Lower Site Risk
Pre-assembled oak frames arrive at the build site with all components clearly marked and ready to go. This simplifies the installation process and reduces the margin for error, because each element has already been test-fitted in the workshop. There should be no need to make on-the-fly adjustments or troubleshoot tricky joints mid-assembly.
Is Off-Site Construction Right for Every Project?
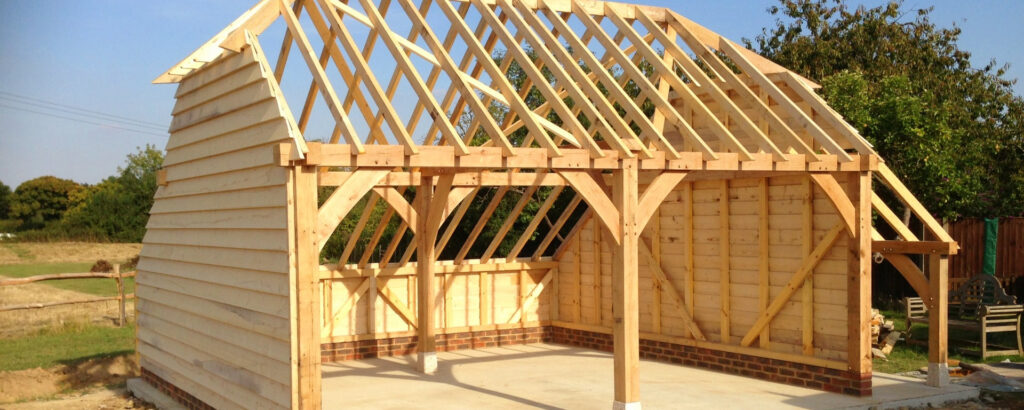
Off-site construction is ideal for a wide range of oak-framed buildings. Home offices, garages, garden rooms, porches, and other outbuildings are perfect candidates – especially when built to a standard or semi-bespoke design.
However, it may not suit every situation. Sites with extremely limited access, unusual terrain, or highly bespoke alterations required during construction can present challenges. In these cases, elements of the frame may still need to be adapted on-site.
That said, for most residential projects, off-site construction offers an excellent balance of quality and convenience – particularly when paired with expert planning and design from the outset.
Planning Considerations
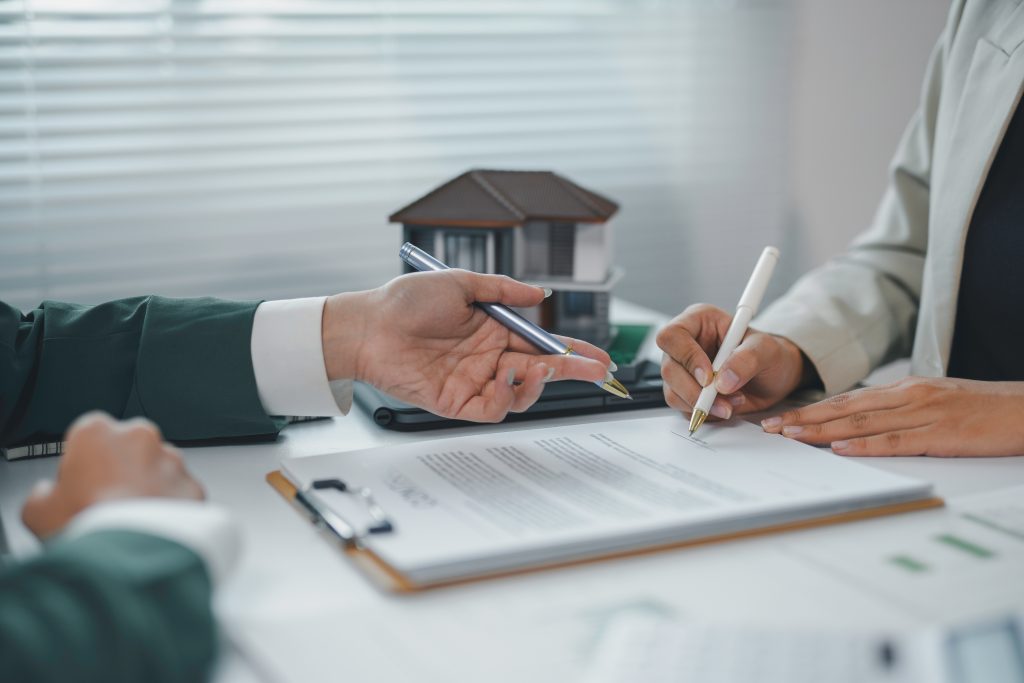
Off-site construction doesn’t alter your planning requirements – it’s simply a smarter way to build. The same rules apply whether your oak frame is built on-site or pre-assembled in a workshop. However, because off-site builds are typically quicker and tidier to erect, they can simplify the planning process in practice.
Many smaller oak-framed structures, such as garages, garden offices or annexes, may fall under permitted development, meaning you won’t need full planning permission if size and siting conditions are met. It’s always wise to check with your local planning authority, though, especially if your property is in a conservation area or Area of Outstanding Natural Beauty.
We are happy to help guide you through these early steps if you need us.
Build Better, Faster, Smarter Oak-Framed Structures
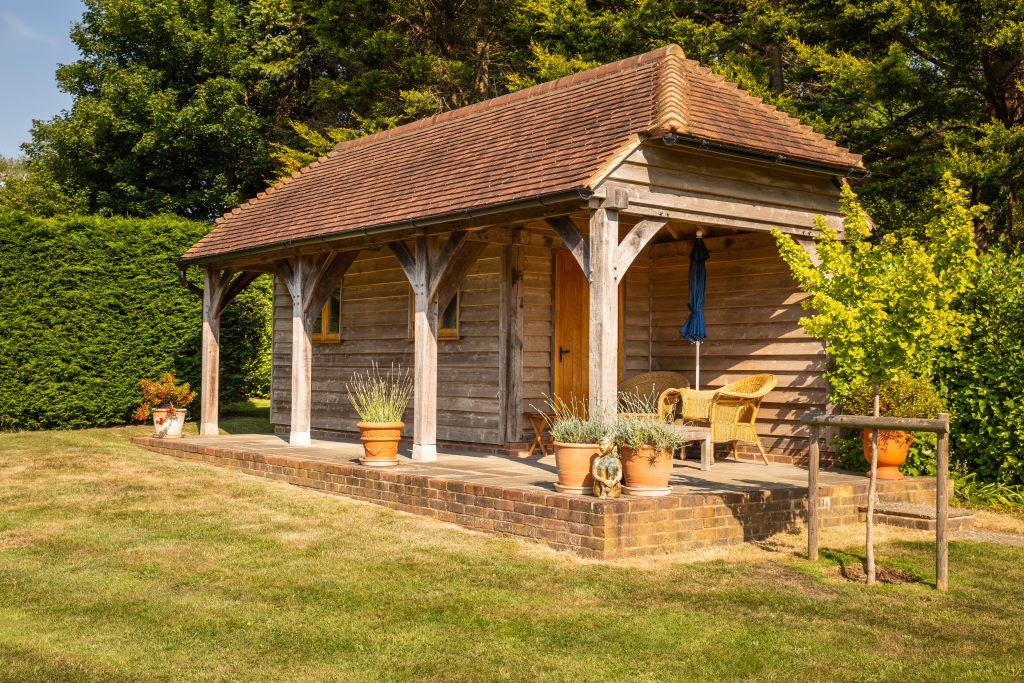
For those of you seeking a smooth, efficient build without compromising on quality or character, off-site construction offers clear advantages. From precision joinery to faster installation, it’s a method that brings real peace of mind.
To explore the possibilities for your own project, browse our oak-framed building range or get in touch with the team to discuss how off-site construction could work for you.